Unicamp: Pesquisador cria método mais simples e barato para fabricar fibras ópticas
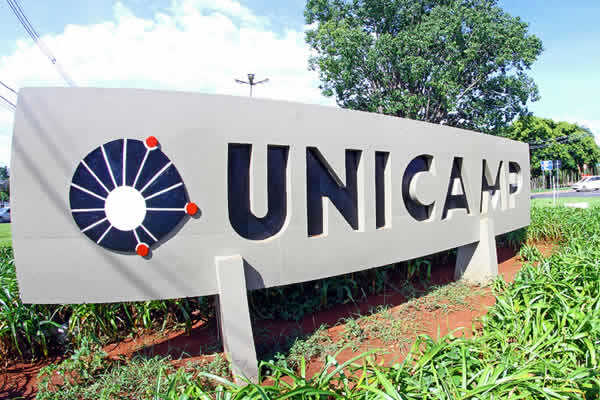
Um novo processo de fabricação de fibras ópticas especiais – muito mais simples, rápido e barato do que os tradicionais – foi desenvolvido pelo pesquisador Cristiano Cordeiro, professor do Instituto de Física da Universidade Estadual de Campinas (IFGW-Unicamp).
O cientista criou o método durante estágio de pesquisa na University of Adelaide, na Austrália, apoiado por bolsa da Fundação de Amparo à Pesquisa do Estado de São Paulo (Fapesp), em parceria com Heike Ebendorff-Heidepriem. Um artigo, assinado pelos dois e mais um colaborador, foi publicado no periódico Scientific Reports, do grupo Nature.
“O processo convencional necessita de um equipamento enorme e extremamente caro. E demanda quase uma semana de trabalho. Nosso processo pode ser realizado com um equipamento de bancada, no mínimo 100 vezes mais barato. E vai do grão de polímero à fibra microestruturada pronta em menos de uma hora. Com ele, muito mais pesquisadores e laboratórios estarão em condições de produzir suas próprias fibras ópticas”, diz Cordeiro à Agência Fapesp.
Em linhas gerais, o procedimento é semelhante ao método de extrusão utilizado na fabricação de macarrões: uma massa mole é pressionada e empurrada através de um molde; e o fio, com sua estrutura interna, sai pela outra ponta. “Evidentemente, tudo isso é feito com muito maior rigor e precisão”, sublinha o pesquisador.
Dados
Centenas de milhões de quilômetros de fibras ópticas estão instaladas atualmente no planeta. E a quantidade de dados que transportam dobra aproximadamente a cada dois anos. Além de seu uso em comunicações, as fibras ópticas são empregadas também no sensoriamento remoto, possibilitando a monitoração de grandezas como temperatura, tração mecânica, pressão hidrostática e escoamento de fluidos.
Devido à robustez e pequeno diâmetro, têm sido utilizadas com êxito em ambientes hostis e de difícil acesso. Daí a importância de inovar os métodos de fabricação.
“A produção convencional exige uma sequência de etapas e equipamentos de alta complexidade, como a torre de fabricação. É preciso, primeiro, criar uma versão macroscópica da fibra, com dois a dez centímetros de diâmetro. Essa estrutura é então aquecida e controladamente tracionada pela torre de fabricação”, descreve Cordeiro.
“A massa se conserva, e o diâmetro diminui enquanto o comprimento aumenta. Nosso método simplifica e barateia enormemente o procedimento. Alimentado com grãos de polímero, o dispositivo que concebemos vai da matéria-prima ao produto final em uma única etapa”, ressalta o cientista.
Fabricação
O procedimento permite fabricar não apenas as fibras totalmente sólidas, nas quais a luz é transmitida por meio de um núcleo com maior índice de refração. Mas também as fibras microestruturadas, que possuem um arranjo de buracos paralelos ao eixo longitudinal, possibilitando maior controle das propriedades ópticas e mais funcionalidades, incluindo a oportunidade de guiar luz com baixa perda de energia em um canal de ar. Para criar as microestruturas, os pesquisadores empregam moldes de titânio com desenhos apropriados.
“Para simplificar a fabricação das fibras ópticas especiais, utilizamos equipamentos e técnicas que têm ficado cada vez mais baratos e corriqueiros devido à popularização das impressoras 3D. O único equipamento usado é uma extrusora horizontal, semelhante às empregadas na fabricação de filamentos para impressoras 3D. Esse dispositivo, não maior do que um forno de micro-ondas, tem custo extremamente reduzido quando comparado com a torre de fabricação. O molde de titânio, com partes sólidas e orifícios, é acoplado na saída da extrusora”, pontua Cordeiro.
Em razão da intrincada estrutura interna, os pesquisadores produziram os moldes por meio de manufatura aditiva, utilizando impressoras 3D apropriadas. Vale destacar que este tipo de serviço de manufatura pode ser contratado a empresas especializadas, de modo que o único equipamento necessário para a fabricação da fibra é mesmo a extrusora horizontal.